“The Technoimpianti brand is synonymous with quality and reliability in the hazardous goods sector. Our products constitute a clear reference point for all national and international markets. Technological advances and dedication to future safety and security are challenges that we face every day. To this end Technoimpianti continuously modernises and expands its product range. Client satisfaction is our most significant corporate asset.”
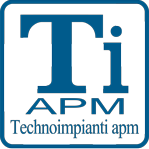
In 1980 we were trading as Technoimpianti (Pty) Ltd with the goal of equipping industrial vehicles, providing consultancy services to small and medium manufacturers in the sector, including primary engineering services, in outsourcing for major corporation in the Oil and Gas industry.
Thereafter, we started manufacturing tanks for transporting hazardous goods relying on the use of outside workshops to produce our designs.
In 1997 we began our own internal manufacturing production as well as revamping, mostly of tanks for cryogenic transport, at our plant at Solza (BG): and so Technoimpianti A.P.M. (Pty) Ltd was launched.
In 2007 we acquired the manufacturing capacity and the brand Bevilacqua Costruzioni Impianti Ltd, corporate leader in the LPG market with headquarters at Pioltello (MI).
In 2015 we inaugurated our new offices at Medolago (BG), a significant investment further impelling the company towards future opportunities.
In 2022 we made a further significant investment with the purpose of transferring all our manufacturing capacity to one site at Suisio, which will be the new headquarters from 2023.
Production is currently focused on three principal lines: cryogenics, liquefied and compressed gas. The goals we pursue daily are as simple as they are ambitious: excellence should be in our DNA. We aim to remain as leaders in the hazardous goods field and to be a valued and reliable partner for our clients.
MedolagoBergamo
These are our headquarters where our management, administration, technical and commercial offices, procurement and quality control services are located. Production takes place over approximately 2 500 m² under roof, including a sandblasting plant, a powder coating oven, four overhead gantry cranes with an overall capacity of 40 tonnes, a test facility for regulating medium and high pressure, cryogenic pumps, a calibration unit for LPG measuring instruments, a workshop for calibration of safety valves, a barcode facility of 300 m², cleaning apparatus for oxygen equipment, high vacuum and ultra-high vacuum pumps and all the latest equipment presently available for use in this specific sector.
PioltelloMilan
This former headquarters of Bevilacqua C.I. is now the boiler-making facility of the group. All pressure tanks, whether fixed or mobile, or in carbon steel or stainless steel are manufactured and tested in an area of 3 000 m² under roof enclosing six overhead gantry cranes with an overall capacity of 110 tonnes; an oxy-acetylene/plasma industrial cutting plant of 14x3,5 metric tonnes, a rolling press with three laminate rollers of 3 000x25 mm max, two submerged arc-welding plants and the best state-of-the-art machinery available on the market.
SuisioBergamo
The new centre where TiApm’s products will be made, is being built over a total area of approximately 20 000 m² including a manufacturing area of 6 000 m² fitted with photovoltaic units and office space of 400 m², with an external warehouse and storage space for stock and for production lines for current corporate needs.